Reverse Engineering
Reverse engineering can be explained as going backwards from the end product to the
design stage by using digitization techniques while in conventional product development the
process is from the design stage towards the end product. (Product development: Induction Reverse Engineering: Deduction)
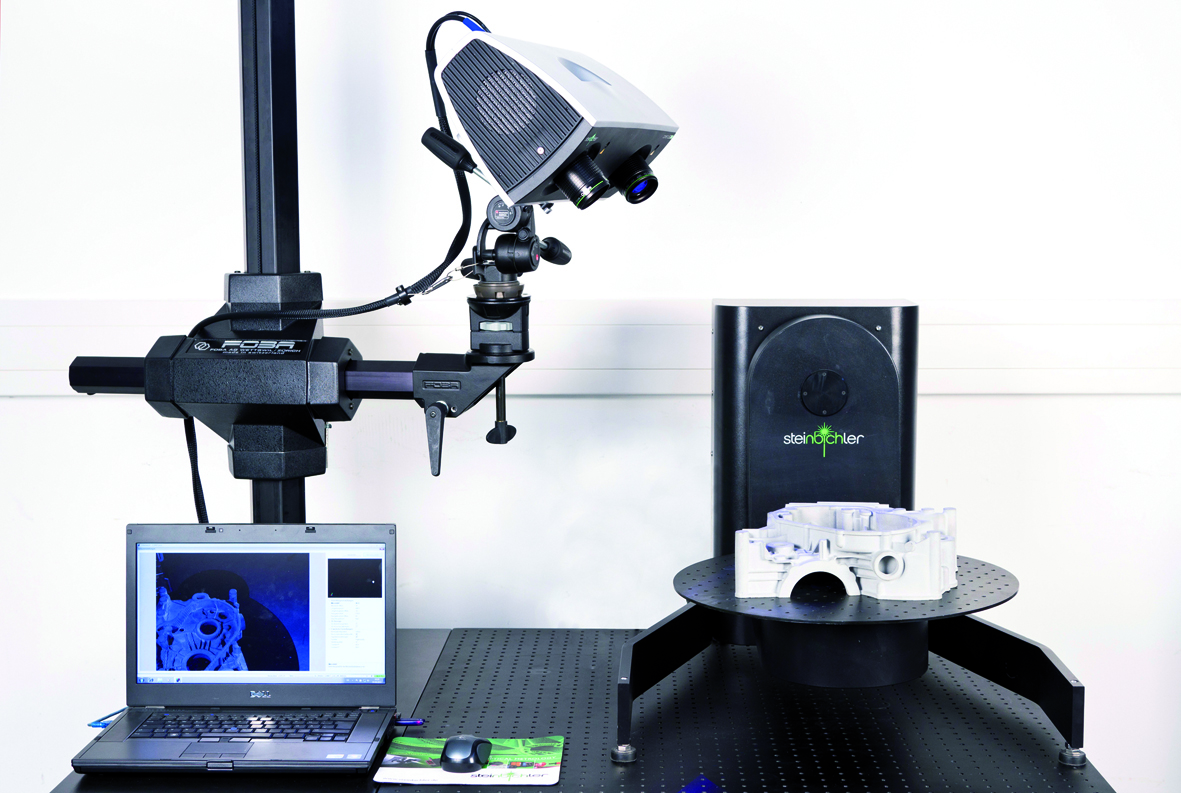
Conventional engineering which includes stages proceeding from design towards the end
product is called forward engineering. The engineering methodology that is directed from
the end product back to the design stage is called reverse engineering.
Although reverse engineering operations in engineering may be regarded as copying, it
would be incorrect to define this discipline only as 3D part scan. The main purpose of reverse
engineering is to check the product geometry and conformity, and to understand its working
mechanism.
When measuring instruments such as micrometer caliper are not sufficient in geometrical
reverse engineering activities, the parts are digitized by scanning with 3D measuring devices.
The parts can be analyzed, developed, and even made producible with the design
information. It is also possible to increase the efficiency of the product with the design
obtained by 3D scanners.
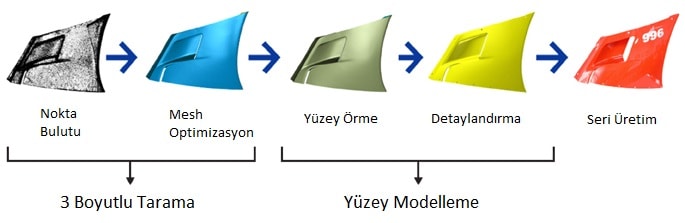
In design generation practices, the reverse engineering process includes three phases:
- 3D Digitization (3D Scanning)
- Point Cloud preparation (Triangulation/Mesh Optimization)
- Surface generation
Usage fields of Reverse Engineering:
- Identification of variables that affect product performance (such as geometry, dimensions
etc.) and the improvement of relevant variables
- Digitization of the clay model made by hand in the industrial design stage
- The necessity of re-manufacturing out-of- production items
- Comparison practices amongst similar products - Benchmarking
- Scanning the object for direct prototype production
- 3D data derivation from product, mold, tool, and machine parts
- Mold creation in dental and medical applications
- Environment, object or human scanning in virtual reality applications
- 3D design creation of figures, sculptures, constructions, artworks etc. in restoration work.
Comparison of 3D data before and after restoration
- Measuremental and dimensional quality control practices after mass production
- Determining springback observed at parts formed in sheet metal dies.
- Measuring the dimensions and warpage of the product produced in plastic injection mold.
- Determining wear at molds / dies and parts over time.
- Scanning deformed parts taken out of mold and re-machining the mold to obtain a pre-
deformation to compensate that defect.
- Data recovery for products, molds, artworks whose design data is lost.